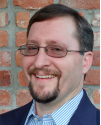
An essential element in Lean thinking is Kaizen. Kaizen is the Japanese word for continuous improvement or change for the better. It’s a tool to make work easier, safer, and more productive by studying a process, identifying waste, and applying small incremental improvements that ensure the highest quality. As no process can ever be declared perfect, there is always room for improvement. Kaizen involves building on gains by continuing experimentation and innovation.
From my experience there are some golden rules to make your kaizen successful:
1. Kaizen starts with the three “actual” rule.
• Go to the actual place where the process is performed.
• Talk to the actual people involved in the process and get the real facts.
• Observe and chart the actual process. (Improvement is not made from a conference room.)
2. Ask why (five times) to get to the root cause.
3. Base decisions on data, not opinions.
4. Try-storming
•Don’t spend too much time talking about a solution, try it!
•It’s okay to fail early on as long as you learn from your mistakes.
5. Value of the team
•Listen to the operators, your team, and your customers.
6. Don’t seek perfection. This will be obtained one step at a time.
7. Think of a new method that works. Throw out all your old fixed ideas on how to do things.
8. Creativity before capital. Don’t substitute money for thinking.
9. Think safety during the Kaizen, both for employee and process.
10. Assure a quality product will be consistently produced through standardization and process controls.
Not all techniques will work for everyone the same way. Acknowledge what you learn and use what is useful to you. Improvement is made from action. All improvements must be maintained if we wish to secure consistent gains. Think of the smallest step you can take every day that would move you incrementally towards your goal. ■
Republished with permission from Tim McMahon. Tim McMahon is a Lean implementation leader, author, and blogger. He is the founder and contributor of A Lean Journey blog. This site is dedicated to sharing lessons and experiences along the Lean Journey in the Quest for True North. As a Lean practitioner, Tim brings nearly 20 years of leadership experience implementing Lean manufacturing. He has held a number of leadership positions within operations management, Lean, and quality disciplines of innovative high tech manufacturing companies. Tim has a passion for teaching problem solving skills, Lean philosophy, and quality improvement methods by actively learning, thinking, and engaging people. Read more of Tim’s work at http://www.aleanjourney.com/.
By Tim McMahon