Silicon Valley Mechanical (SVM) is a mechanical contractor located in the Silicon Valley, serving an area reaching from South Bay to the Peninsula. The company fabricates and installs complex HVAC and plumbing systems in various building types, ranging from commercial uses to high-tech facilities, and including educational and high-density residential clients. SVM specializes in true design-build, taking on the most complex tenant improvements, clean rooms, laboratories, and data centers. It also runs a 24-hour emergency service team.
The company has experienced incredible growth over the past five years, employing over 750 employees consisting of 650 field and production union members and 100 office personnel. When SVM first implemented BuildCentrix, it was a team of 100 field and 15 office employees, but management saw growth on the horizon.
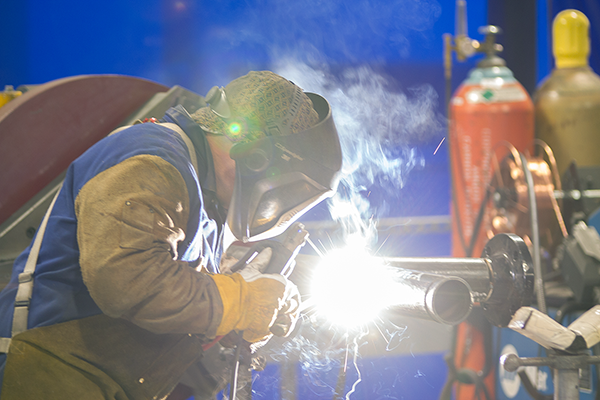
Silicon Valley Mechanical currently uses BuildCentrix’s field ordering and timecard modules. That means field personnel can use live, database-driven ordering to select components from an extensive library of SMACNA standard components and fittings, and digitally enter hours worked in a fraction of the time it would take to record them manually.
Prior to using BuildCentrix, SVM did its ordering and time tracking by hand. “To order, our field would send hand-drawn fittings on cut sheets, which then had to be entered into the system,” says Jeremy Day, field operations manager for SVM. “This took a lot of time for the inputter and left a lot of room for error.”
The BuildCentrix implementation means components are selected from a library and parameters on the system ensure nothing can be constructed outside of SMACNA’s stringent fitting standards.
The timecard installation was successful for similar reasons. “We used a combination of Excel spreadsheets and handwritten forms that were then entered manually into our payroll system by the our payroll team,” says Hannah Monteiro, administrative operations manager for SVM. “Approvals by our superintendents took more time, job costing errors were easily missed until payroll entered the information, and the overall time to process payroll was significantly higher.”
The BuildCentrix installation has changed that process so personnel can enter hours worked from a digital device, and the information is integrated seamlessly with the company’s payroll system.
From a production standpoint, BuildCentrix has improved communication between the field and shop, eliminated the time wasted deciphering incorrectly drawn fittings, and reduced time spent reviewing orders for accuracy and errors. “Now, the employees report their time directly using a tablet, which has replaced the need to create, fill out, and manage manual forms,” says Monteiro. “Our superintendents now spend a fraction of the time approving their teams’ hours by using the BuildCentrix upload feature.”
As a tech-savvy, forward-thinking company, the decision to use BuildCentrix to automate these key processes wasn’t a difficult one, and in looking back, the implementation occurred at just the right time.
“We had just over 100 employees at the time, so the implementation was not difficult,” says Monteiro. “There was a learning curve for each employee, but they all accepted the program after one or two training sessions.”
Day and BuildCentrix’s vice-president of operations James Beveridge are currently working on taking the data collected from the field ordering and payroll modules and implementing it to help measure how many pounds of metal are fabricated per hour, which will help measure and assess the company’s productivity rate.
“We look forward to seeing more integration with third-party vendors, such as Vista and CAMDuct in the future,” says Monteiro. “I don’t have the time to sit down and review long reports, let alone build them,” says Day. “As SVM focuses on improving efficiencies, we need fast and powerful reporting. Being able to look at visual reports like what BuildCentrix offers gives me real time data in a format that easy to digest. We can take that information to set benchmarks and look at improving productivity.”
As a company that has experienced exponential growth over the past five years, SVM is in the best possible position to benefit from a program like BuildCentrix because it saves time and costs and frees up company staff to do the things they are best at. This is a growing trend in full-service mechanical contracting firms keen on responding to market forces.
“Without a program like BuildCentrix, we wouldn’t have the competitive edge to meet SMACNA standards in a cost effective timeframe while reducing manhours spent on administrative tasks,” says Monteiro. “You have to figure out how to minimize time spent doing things that take away from the quality of your work. ▪