BuildCentrix now has pre-fabrication capability in its 3D Take-off Builder for quick and easy pre-fab component take-offs
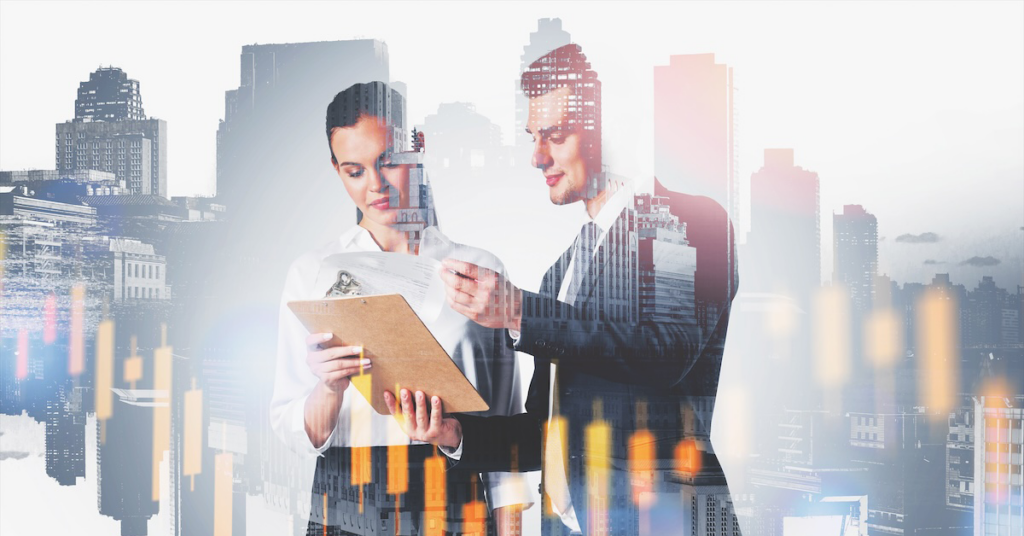
Mechanical contractors are more commonly looking to prefabrication to save time, costs, and logistical challenges onsite. Why aren’t you? Moving more of the work into the shop and shipping completed segments to the field for installation changes the labor requirement, increases productivity, reduces safety risks, and lowers overall project costs. In fact, according to the Modular Building Institute, prefabricating components offsite can deliver a project 30% to 50% faster than traditional methods.
By nature, mechanical projects have a lot of moving parts, starting with multiple trades on the jobsite at once. These high-volume, heavily trafficked work areas open up a world of potential safety hazards as each trade develops its own workflow—and they don’t always jive with others’.
“Off-site fabrication mitigates a number of these issues,” says James Beveridge, CEO at BuildCentrix. “Duct, piping, and heating/cooling assemblies fabricated in the controlled and specific shop environments—often automated—are created in less time and with less risk, minimizing human error and wasted materials.”
Prefabrication also creates a more predictable environment, so contractors can better estimate the time and cost of a project and help it stay on schedule and on budget.
Productive teams
From a teams perspective, the Lean Construction Institute says prefabrication is well suited to integrated project delivery (IPD), “since these projects require early alignment of the project team, providing the team the opportunity to plan the project scope and budget before design begins.”
IPD facilitates the best possible value for the owner, including whether the specific components, assemblies, and modules could be prefabricated prior to their arrival at the construction site. In its “Integrated Project Delivery Ultimate Guide,” LCI lists five essential steps to implementing prefabrication into a project, and points to mechanical components as some of the best fitting for prefabrication.
“Consider prefabrication for repetitive elements of a building and complex elements that can be produced more accurately, productively, and safely under controlled factory conditions,” says the guide. “These elements include single-trade assemblies, such as preassembled plumbing stacks for bathrooms or panelized exterior curtain wall; and multi-trade assemblies, such as above-corridor racks containing ductwork, plumbing piping, power conduit, and low-voltage cable trays.”
Getting it right
The construction industry knows the value of prefabrication, but doing it well requires specific considerations. For example, prefab contractors need detailed, accurate knowledge of the construction site, shared scheduling information between trades, and solid in-house technology.
“One major issue involves discrepancies between the project blueprints and what is actually happening on the site,” Beveridge says. “If change orders aren’t adequately reported to all team members, this can result in significant time, cost, and labor expenses if components are incorrectly sized or manufactured. Say goodbye to the budget and schedule.”
Good tech, great results
A prefab environment relies on the growing use of digital and automated systems. Building information modeling simplifies the move to prefab, and shop technology is allowing users to create more sophisticated and flexible prefab assemblies.
Driven by customer demand, prefab functionality within the 3D Take-off Builder in BuildCentrix is a game-changer for contractors. It efficiently captures accurate and complete jobsite details and, because all information is shared and updated in real time, the entire team is immediately aware of change orders.
The Blueprint Upload feature allows users to upload blueprints to the platform and take-off components overtop the digital blueprint file. This ensures accuracy and complete jobsite and project details and allows users quick and accurate access to these details in the event of a change order.
Integrated, up-to-the-minute information is sharable across the platform, facilitating communication and collaboration between departments. With everyone on board and in the know, errors are less likely, and prefabrication can begin without rework down the road.
“Prefabrication is synonymous with standardization and created in a controlled environment, and standardized components are the Holy Grail of quality work,” Beveridge says. “In-house checks halve the defect rate, and the defect-free rate on new buildings is typically above 95% on projects using prefabricated components.”
ShoffnerKalthoff MES, Inc
ShoffnerKalthoff MES, Inc (SKMES) is a mechanical, electrical, and plumbing (MEP) contractor that has installed many of the most complex mechanical, electrical, and plumbing systems in east Tennessee, southwest Virginia, and the western Carolinas.
SKMES offers extensive construction services, including electrical, mechanical, and industrial construction capabilities, and full manufacturing services, including sheet metal, spiral duct, processed pipe, and custom stainless steel fabrication.
Its prefabrication shops for sheet metal ductwork, plumbing, mechanical, and process piping enable projects to continue no matter the weather or storage and fabrication areas on a jobsite.
“Our ability to prefabricate almost anything, from stainless and carbon steel to mechanical and food grade piping, makes us the perfect choice for all manufacturing needs,” says William West, industrial manager for SKMES.
He says the ability to prefabricate virtually anything customers require has allowed the company to perform more work in the field with less humanpower and with greater efficiency.
“In terms of productivity, we can perform the work in a controlled environment, which helps us increase productivity and reduce waste,” he says. “With rising material and labor costs, it is very important to us to be productive.”
Prefabrication means planning and logistics take a larger role, due to the amount of pre-planning required to manufacture and ship the components. Logistics, delivering the assemblies, and scheduling time to pre-plan the work can become pain points.
“It is very important to have technology to support our prefabrication efforts,” West says. “With the addition of prefab capabilities in BCX, we will be able to order our assemblies electronically instead of wasting time manually drawing them. This should also eliminate some errors in the manual orders.
“Prefab has been a focus of SKMES for many years now,” he adds, “and it is great to see technology begin to catch up with the trades.”
Start benefiting from prefab
From saving time and money to creating a safer work environment, making prefab part of your production processes is a fast and easy way to improve project performance and results.
“Start saving time in the field by doing more assembly in the controlled environment of the shop, so field personnel just have to lift the pieces into place on the jobsite,” Beveridge says. “The new tools from BuildCentrix can help make the process seamless.” ■
Schedule your free demo with BuildCentrix today at buildcentrix.com