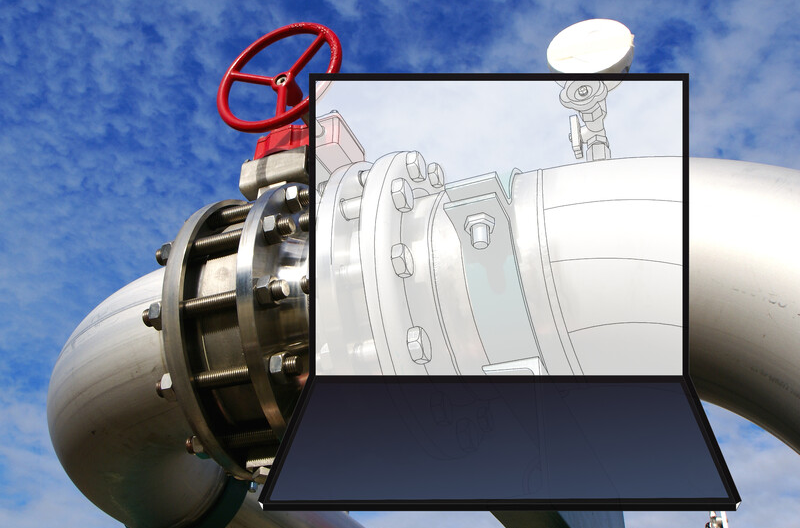
Collaborative building design is firmly entrenched in the digital world and this is where it will continue to grow and shed redundancies. As building information modelling (BIM) has grown in popularity and usefulness over the past decade, so has the proliferation of software to control the manufacturing process and that is a positive for the industry … until it isn’t.
Up until now, manufacturing has followed a consistent process: design files are pulled from CAD and sent to programming software, which calculates the parameters of the job and generates instructions for the machine. The process is supported by intermediate software in various configurations and on various computers, generating the correct algorithms for the specific machines. In this regard, CAD/RevIt (the model) and the machines are separate entities limited by the scope and ability of software and operating in a multi-user environment. This once-revolutionary technology becomes a hindrance when processes occur in isolation and the specifications of one piece of software don’t quite align with another.
Technology moving forward will change all of that. Software installed on personal computers and shared in an office environment will be a thing of the past, and the model will speak directly to the machine. In intermediary processing, control, and associated files will be stored in the cloud and anyone with permission will be able to access then. That means collaboration on a whole new level as design, changes, feedback, and interaction occur in real time. Redundancies are eliminated, inconsistencies are a vague memory, and timelines, productivity, and cost schedules enjoy a prosperous future.
Getting there won’t be seamless, but it is coming. Model to machine is about taking the content out of the model, and being able to send it directly to the equipment on the shop floor with no re-work. Doing that requires sophisticated algorithms to determine fabrication standards, and it requires equipment manufacturers to update how they operate—and move to the cloud.
New programming software will have to focus on how to speak to and for the machines and the focus will have to shift to what the customers requires–Quality? Cost savings? Time control? Combined with the practical elements of the manufacturing process, the sky’s the limit. The model is brought to life and everything is connected from the architect’s vision to the manufacturing and construction process, and it’s all available to experience in real time.
The long-term benefits of owners having a digital copy of their building are plentiful, and in the new system all the changes and components of the project will be available and archived where they can be reviewed and studied to improve productivity moving forward. BIM helps building owners and operators gain efficiencies during all stages of a building’s life cycle, reduce time delays, and minimize materials waste and cost overruns.
The push towards collaborative BIM has been growing every year. For mechanical contractors looking to pre-fabricate components within their shops, BIM can be leveraged to group spools or assemblies together, reducing person hours on the job site.
In the mechanical contractor’s current workflow there is a significant amount of work that happens between the model and the machine. Autodesk Forge APIs offer the ability to better harvest data out of the model and eliminate some of the redundancy in these processes, and the more mechanical contractors can implement a manufacturing workflow the more time they can save on site and in the shop by creating a standardized library of parts, getting rid of costly custom fabrication, and gaining efficiency through volume of similar parts.
No more CAM middleware and manually scanning or updating statuses. Rather, there should be a fabrication management tool for scheduling, tracking, reporting, and the equipment should be able to automate how they grab and communicate with fabrication content.
Currently, most shops are in the dark regarding fabrication from the model. Being able to accurately measure the backlog of work and see in advance of what they have next allows mechanical shops to behave like manufacturers and plan their work accordingly. Although it’s not possible to pinpoint what this will look like in exact terms, there is no doubt it is coming.
Are you ready?
By Jessica Kirby